The use of radio frequency identification (RFID) technology is expanding across a wide range of industries.
One of the largest industries using RFID in various areas of their supply and manufacturing chains is the automotive industry. Some well-known automakers have been using RFID technology for a long time and are getting the benefits of it.
HOW it WORKS
1. TAG ITEMS
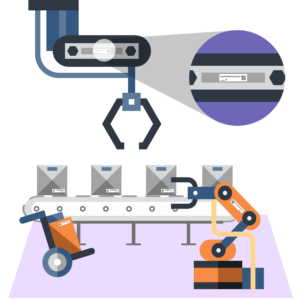
RFID tags are attached to assets. Since many of the assets Can be metallic, special metallic rugged tags can be applied on those assets. RFID tags also provide a unique identifier for each of these assets.
2. RFID READERS
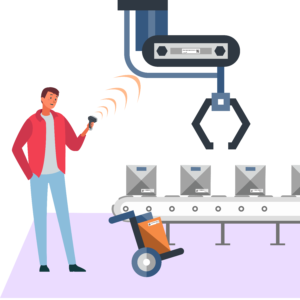
Throughout the asset’s operational workflow, automate the data collecting with RFID. Tools can be swiftly checked in and out using RFID, for instance. Use RFID readers’ and handhelds’ capabilities to track asset presence and mobility in important locations.
3. RFID MAINTENANCE
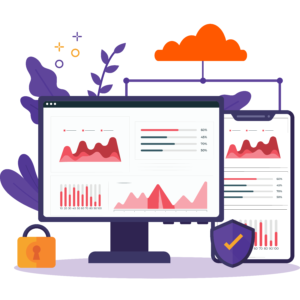
Use RFID tags to identify the asset when it needs maintenance or repair. Data can sometimes be immediately written to the RFID tag in particular circumstances. In others, the RFID tag can serve as a unique identifier for the asset so it can be quickly and accurately identified in a database.
This technology is giving more precise control and boosts operational effectiveness throughout whole supply chains and manufacturing activities including:
Shipping and Receiving: It’s typical for new parts and components to continually arrive from various suppliers. It is required to monitor all parts received are correct and in the right quantities. Also, it is very important to send the release the right shipment with correct parts and without missing it. RFID facilitates movement tracking when shipping or receiving any parts.
Tool Tracking: RFID not only makes it possible to locate tool in real time, but it may also, to a certain extent, prevent specialized tools from leaving a certain area.
Work in Progress: RFID can be used in the automotive industry in all aspects, whether it is tire manufacturing, vehicle glass manufacturing, steering manufacturing, or any other part. Since complete assembly involves different sections, it is important to know that the correct parts are moving forward to minimize the risk of failure and save time. RFID tags can be attached to parts and tracked at each stage of the assembly process.
Vehicle Tracking: RFID label can be assigned to an assembled vehicle with a unique serial number along with other associated data like manufacturing history. Complete information can be retrieved about the vehicle by just reading the RFID tag and can also ensure the correct destination where the vehicle was shipped.
Returnable Containers: In the Automotive industry, RFID technology plays a crucial role to control returnable containers. Within the automotive supply chain, containers are transported and stored in returnable containers like bins, pallets, and other transport items. In this context, RFID offers several advantages including Real-time visibility, automated tracking and identification, streamlined supply chain procedures, improved traceability, and effective inventory management. This makes it possible to plan more effectively, cut down on delays, and boost overall productivity in the whole automotive supply chain process.
Dealership: In a report, millions of cars and light trucks are sold every year in the United states. Tracking all the cars was a challenge and then RFID started spreading widely across the country. It not only helped every movement of the cars in their inventory but also service department post sale of the cars.
Tracking Inventory: A dealer may always be aware of how many automobiles are available, how many are in stock, and how much inventory is worth at point of time.
Automation: In RFID enabled systems, reports for each process are automatically collected by passing the parts boxes through an RFID gate. In repacking, workers can check for errors by comparing data from the RFID tags against order information.
RFID also helps in locating vehicles, monitoring test drives, and, most importantly, providing service based on the customer’s past service history and minimizing questions. On the other hand, it speeds up the check-in process and provides more accurate information to the service representatives.
RFID for the production line
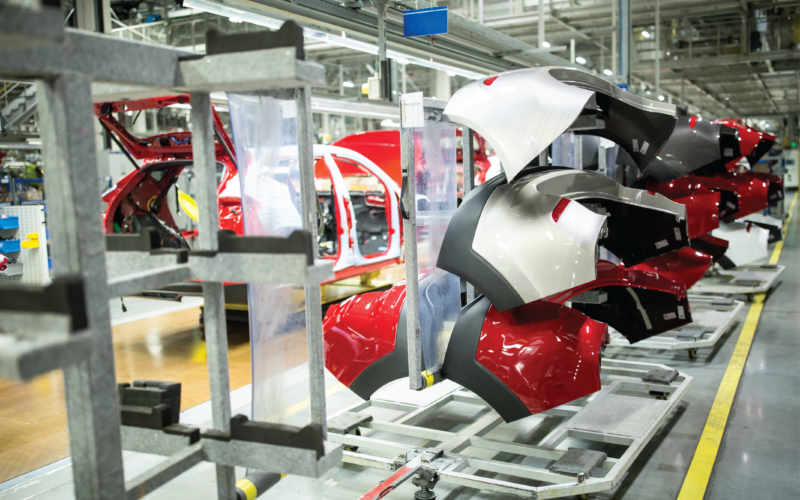
Welding production line: A high-temperature, dust-proof, reusable packaging label or tags are used in the welding production line. Operation instruction information such as vehicle type information, welding instruction information is stored in it. With the result, errors are highly reduced and control on the internal supply chain gets improved.
Coating production line: Coating production line uses RFID technology to collect a variety of on- site data, status monitoring, and quality inspection information in real-time and promptly transfer it to the production control center.
Assembly line: Manufacturer attaches recyclable and reusable RFID tags on assembled vehicles. After compiling the relevant serial number for each assembled vehicle, a serial number into the RFID tag is written. Put the reader in the proper location at each workstation, read the tags to cross check and guarantee that it was assembled correctly at every station along the assembly line.
Conclusion: To stay competitive in today’s automotive manufacturing industry, implementing RFID in the automotive supply chain has become a necessity. RFID4U (https://rfid4u.com/) can reduce inventory management expenses, avoid manufacturing delays, and solve the biggest production problems for automakers and other parties involved in the supply chain.