Explore / RFID Basics & Resources
RFID Basics - RFID Printers Encoders
RFID PRINTERS & SMART LABELS
Every RFID implementation needs peripheral devices such as RFID-enabled printers, RFID-enabled automated label applicators (also known as print and apply devices), as well as feedback components such as light stacks, horns, LED lights or LCD displays, and triggering devices such as light break sensors. These devices enhance the capabilities of an RFID system, control I/O devices, control system timing functions, and provide on/off capabilities for various business applications. Peripherals also improve human interactions with RFID hardware by assisting automatic data collection and increasing the safety of the system.
RFID printers in an automated RFID system often utilize existing print points within a manufacturing or distribution supply chain. Because many of the current Auto-ID systems use barcoding, the conversion to RFID systems will be an incremental change. The first step in enabling your current barcode printing and application points with RFID will be to obtain RFID-enabled label printers.
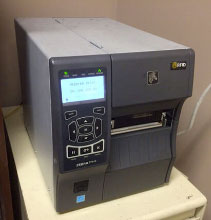
SMART LABEL
RFID-enabled label printers represent a tagging method that can accommodate both types of Auto-ID systems, RFID and barcode, in a single unit. The system uses a regular barcode label with an RFID inlay embedded in the back of the label. This is called a smart label and will typically have human-readable information printed on the front of the label. The addition of the RFID tag enables non–line-of-sight identification, which allows for many automated functions and/or serialized inventory.
Using a smart label printer is the easiest way to handle RFID integration, because it is easily incorporated with the existing business process, data structures, and networks associated with it. The smart label printer replaces the existing printer, keeping the label application process identical. The same print server and network connections used for the old printer can be used with the new one.
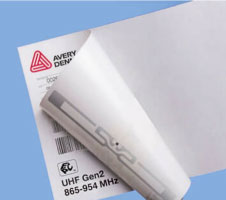
LABEL APPLICATION
Based on the integration of RFID technology within the operations and supply chain, there are two options for tagging items and cases.
SLAP AND SHIP
The labels can be printed and applied immediately prior to shipment to downstream clients. This application, typically called slap and ship, is one of the fastest and easiest ways to comply with any customer mandates. However, slap and ship does not provide any of the benefits of RFID for the user, with the exception of verification of shipping. This is sufficient for a company shipping limited amounts of stock keeping units (SKUs).
DURING MANUFACTURING
However, when companies reach a point at which costs of the manual labor used to apply labels onto products prior to shipping outweigh the costs and benefits of tagging all of their products during manufacturing process in an automated manner, slap and ship systems will become obsolete. If you plan properly, you can reuse much of this equipment in the larger, full-scale implementation.
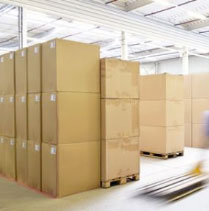
LABEL SELECTION
To use an RFID-enabled label printer, you must first perform a case analysis to determine what tags are correct for use with your application.
CASE ANALYSIS
The labels can be printed and applied immediately prior to shipment to downstream clients. This application, typically called slap and ship, is one of the fastest and easiest ways to comply with any customer mandates. However, slap and ship does not provide any of the benefits of RFID for the user, with the exception of verification of shipping. This is sufficient for a company shipping limited amounts of stock keeping units (SKUs).
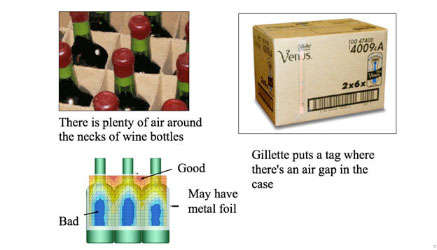
SIZE
The label should be large enough to display all of the existing printed information as well as any additional information required for the RFID tag embedded in the back of the label, such as the EPC logo to indicate the use of an EPC tag within the label. The size should also be appropriate for the boxes to which the labels are applied. You must also consider the compatibility of the label adhesive with the boxes, the method of attachment, the environment in which the tagged assets will be moving, as well as the requirements of the label applicator. The RFID tag embedded in the label should meet pre-existing RFID customer requirements. Some of these requirements can include the standard that the customer uses for reading within the facility, the frequency of operation for the tag, as well as the amount of memory on the tag, read/write capabilities, and the tag’s ability to contain the data required.
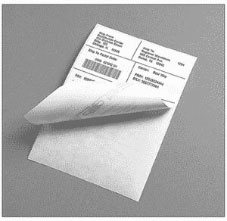
TAG TYPE
The RFID tag embedded in the label should be appropriate for the items inside the box. Special tags may be needed to tag difficult-to-read materials such as water, metal, and most aqueous liquids, as well as packaging or product with high carbon or salt contents. All of these materials can affect the RF signals coming from the interrogator as they attempt to energize the tag.
COMPATIBILITY WITH APPLICATOR
You must also consider the compatibility of labels with your label applicator, including the dimensions of the label and whether or not they fall within the acceptable parameters for the printer. Two main types of label media formats are used: media roll or fan-fold.
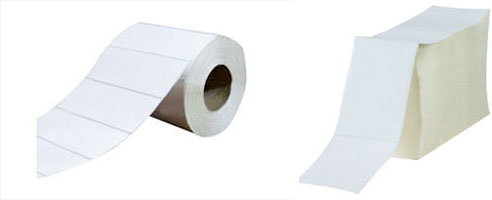
QUALITY
Quality is of prime importance when selecting label stock. This media has to deliver consistent and reliable results. If quality varies dramatically from one roll of media to the next—or, even worse, from one tag to the next—it will make the entire system inefficient. Sufficient time and attention to detail in selecting the proper media is critical to the overall success of any RFID implementation.
PRINT METHODS
The label surface must be appropriate for the method of printing used with the particular printer. Two types of print methods are used for both industrial barcode printers and RFID printers and pros and cons exist for both of these methods.
• Thermal transfer, which uses heat to transfer ink from a separate ribbon to the label. For long-term application where the labels will have a lengthy lifecycle in the supply chain, thermal transfer printers should be used as the labels do not fade with exposure to sun or heat. These printers will typically print with a higher DPI (dot per inch), or resolution, on the label.
• Direct thermal, which uses special media in the form of a treated label stock that turns black when heated. The advantages of a direct thermal printer are a simpler design and therefore easier loading of the media, no ribbon, and easier maintenance for the printer due to fewer components that could break. However, the labels tend to be more expensive and fade quicker when exposed to heat.
Tip: Be aware that for labels that will be subjected to heat, a thermal transfer printer should be used.
INLAY POSITION WITHIN THE LABEL
The RFID tag must be positioned so it aligns correctly with the encoder antenna so that it can be read or written to. This positioning changes from one printer to the next, as many printers have their antennas placed at different locations within the print pad. Each label will be specific to a particular type of printer for which it is designed and the inlay position in the label should match the specifications provided by the printer manufacturer. If the inlay position does not match the required specifications, you will not be able to use a default mode and you will need to run a calibration process to make sure the printer determines the inlay’s position. You can see various tag alignments in the smart label below.
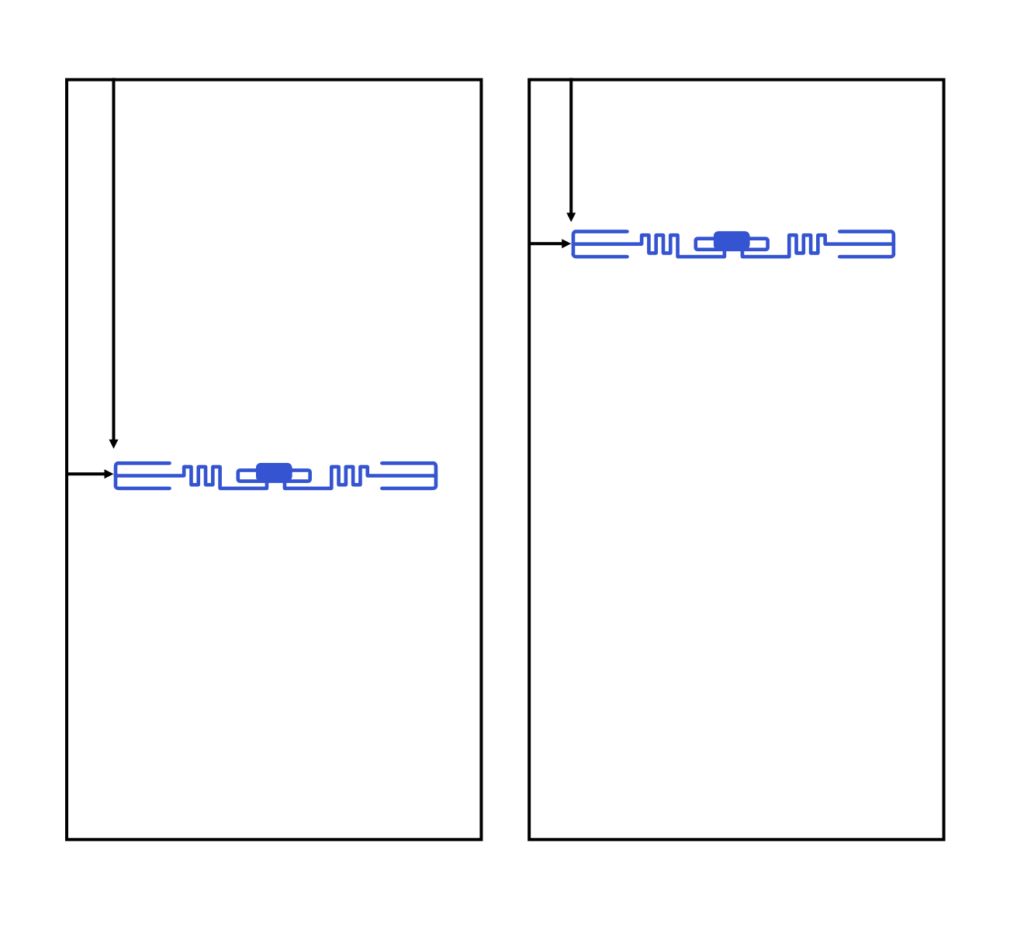
POSSIBLE ISSUES
QUIET TAG
You can encounter a quiet tag. This happens, when a tag inside a label fails to operate within the specifications. Quiet tags can be a major concern for label makers as well as users. Tag quality and performance need to be consistent. If it takes more energy to light one tag than the others, this tag is not going to perform as well in your interrogation zone (IZ). Performance of your tags must be reliable and must have repeatable results that you can count on, in order to properly assess the inventory moving throughout your facility. Most RFID-enabled label printers have a way of verifying the function of the tag in the label and assessing its readiness for use. These printers will determine the response of the tag, and if the tag does not fall within the manufacturer’s suggesting quality guidelines, the tag will be rejected and a special pattern will be printed on the front of the label, indicating it should not be used. The printer will then generate the next available label on the print line.
ESD AND TAG HANDLING
The tag within a smart label contains delicate electronic components and must be handled just as you would handle computer components. Take care to avoid subjecting tags to electrostatic discharge (ESD), crushing, dropping, and exposing to moisture and extreme temperatures. You must consider all of these aspects when choosing proper storage locations and handling procedures before you purchase and use a smart label.
Tip: Most RFID-enabled printers have validation and error recovery built in, and the command structure to control the printer is similar to existing barcode printers, with the addition of RFID control commands to enable the encoding and verification of smart labels.
For more information on Tag Types, review: