Kimbark Laundry
Kimbark Laundry automates check-in and checkout workflow procedures of healthcare scrubs to its customers.
Challenge:
A Chicago based firm, Kimbark Laundry & Dry Cleaning provides services to their customers in the healthcare industry cleaning their surgical scrubs and other garments. The scrubs are picked up from Kimbark’s customers, taken to their faculties for healthcare grade laundry processing and then returned back to the appropriate customer. Since these garments may have been contaminated by infectious diseases, it is not possible to manually count each item by hand when the garments are picked up. However, the ability to count and inventory these items when picked up would provide great benefits, and improve accuracy and overall efficiency.
Solution:
Kimbark Laundry adopted RFID4U’s TagMatiks software to optimize their check-in, checkout and inventory processes. The TagMatiks Heat Seal Laundry tags are attached to garments. Each tag is pre-programmed with a serial number that gives it a unique identity that is linked to a database holding other information about the garment such as the garment type, color, size, owner, department etc. When garments are picked up from customers, RFID handheld scanners are used to scan the bag of soiled laundry and create a complete inventory of the entire contents of that bag.
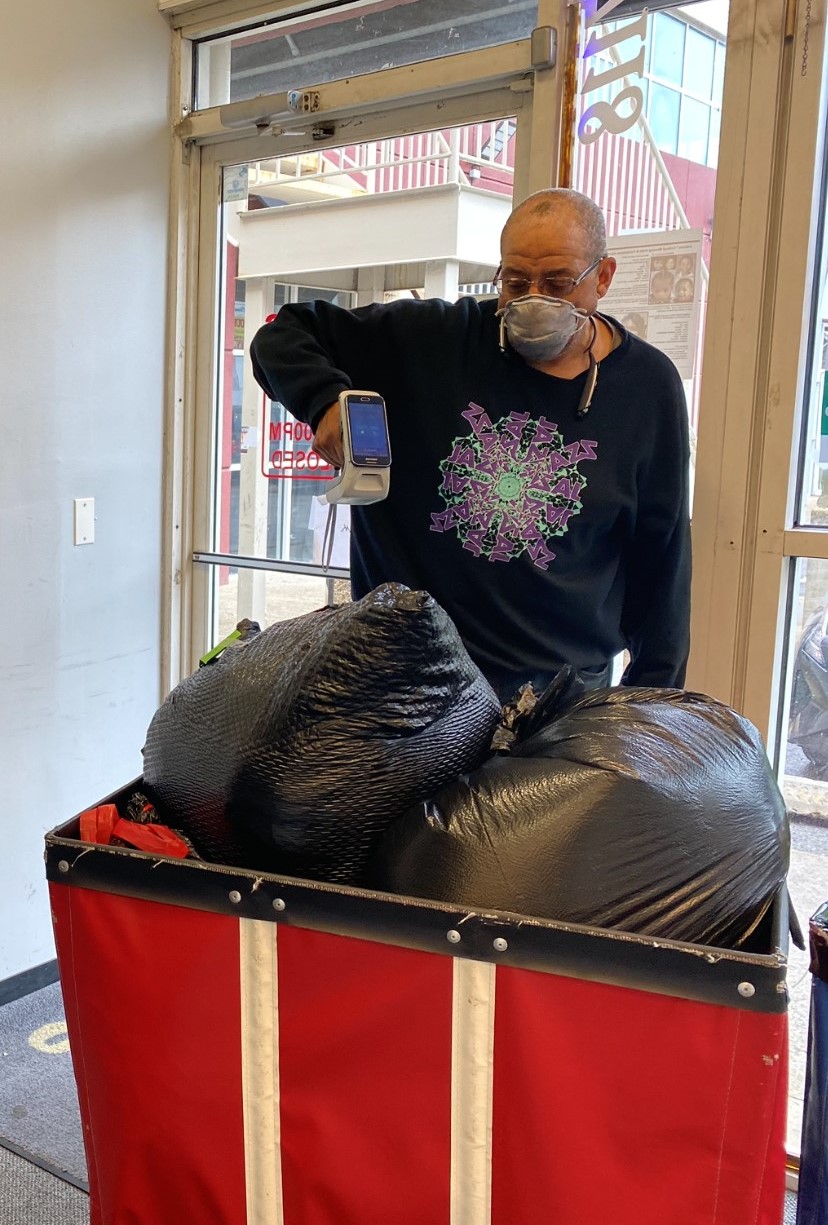
When the garments are ready to be returned to the customer, a second scan is taken. The incoming scan and the outgoing scan are compared to ensure that all garments that were picked up, will also be returned. If there are missing items, a discrepancy report will be generated.
Using the TagMatiks mobile application, Kimbark Laundry is also able to use the accompanying RFID handheld scanners to conduct ad-hoc inventory counts at the customer’s site to verify garments stored in specific locations. The RFID scanners can also be used to find a specific garment by using the “Find” feature.
Result:
With RFID scanners and the TagMatiks system, the traditionally manual processes for check-in and checkout are automated. As RFID technology can capture many items in a single scan, the amount of time to collect data for a pickup or return is drastically reduced. For example, with barcode, the time to count and verify a typical pickup or return may take up to 45 minutes but with RFID technology, the time is cut down to a few seconds with no errors. During these workflows, users don’t also have to find the barcode on the garment as RFID technology can work without “line of sight”.
In addition, there are also safety benefits. When the laundry is picked up, it is unknown what types of infectious diseases may be contaminating the “soiled” garments. With RFID technology, the contents of the laundry bag can be easily verified with a “contact-less” approach and helps keep Kimbark laundry employees safe.
According to Darryl Crawford, owner of Kimbark Laundry & Dry Cleaning:
This solution provides a simple yet powerful approach to automate data collection using sensory technologies like RFID and digitize key workflows. Reports can be quickly generated to help make better business decisions. Leveraging cutting edge technologies like RFID and adopting solutions like the TagMatiks platform helps differentiate Kimbark Laundry and allows them better serve their customer base.